What's Up There?
- Chris Holland
- Jun 3, 2022
- 4 min read
Updated: Jun 5, 2022
Why you should be afraid of the "unknown" items that could be lurking in your ceiling

An often-overlooked pre-construction activity in a commercial interiors construction project in second generation space that can pay dividends, or result in unexpected costs, is an inspection above the ceiling to establish pre-existing conditions that may not have been detailed in construction drawings, notes, or project specifications.
What components exist above the ceiling?
The infrastructure that heats and cools the space, powers equipment, connects the computers, supplies and drains water, and secures the space against fire and uninvited access, generally runs in the ceiling, unless the space has raised flooring that accommodates some of this.
This includes:
Mechanical distribution including duct work and fan boxes.
Electrical conduit and wiring for distribution, including junction-boxes and lighting fixtures.
Fire sprinkler mains, branch lines, and sprinkler heads.
Fire alarm devices and wiring, including detectors, as well as visual and audible alarms.
Infrastructure cabling for technology and audio-visual.
Plumbing lines, drains, and vents.
Security and access controls cabling.

Problems these existing conditions may create
Implementing design specifications can be easily impacted when encountering an "unknown" condition, which can be anything from immovable base building infrastructure to legacy wiring that was not removed from a prior tenant's use.
Common issues include:
Interference with new deck high partitions which may be necessary to demise space, comply with building codes, secure a space, or provide sound attenuation.
Having ample clearance in the plenum space to easily run wiring, conduit, pipes, HVAC equipment, and ductwork.
Creating problems with spacing or placement of new construction components such as lighting, ceiling features, and raised, coved, or vaulted ceiling conditions.
Impeding access to mechanical, electrical, and plumbing component access for maintenance when a drywall ceiling is specified.
Complying with Fire Codes related to the placement of sprinkler heads and coverage based upon the design specifications.
What to look for and why it is important?
Being proactive in gathering information as part of an evaluation of existing conditions above the ceiling will pay dividends in both the design and build phases of the project saving both time, and money. Here is a list of a few things you should look for and why they are important:
Plenum spacing is the amount of space between the top of the ceiling and the slab deck of the floor above. The amount of space available in that area is typically 36" to 48", depending on the ceiling height from the floor. Space in the plenum can dictate the type of ceiling that can be used, lighting, and more. Less space can mean that certain features are not feasible without design changes or result in additional costs to accommodate these conditions.
Virtually all building components require maintenance access. If they are located within the boundaries of a new scheduled drywall ceiling, deeming the area inaccessible, an alternative solution will be necessary. Either the ceiling type changes, the affected components will need to be relocated to accessible ceiling areas (adding project costs), or an accessible solution such as an access panel is necessary.
Electrical box labeling is necessary for tracing and confirming available circuits and designations relative to the as-built drawings, which are used as a baseline for design. If any designations are incorrect or mislabeled, additional costs can potentially be incurred even after a project has started in order to address the conflict.
HVAC equipment, including air handling units, may not be located according to the as-built drawings. Confirming their locations prior to design can save on costs as the difference can be addressed at the time of contractor pricing, rather than incurring additional expenses to relocate these units during the project.
Understanding Fire sprinkler main and branch line clearances can help determine the locations of scheduled lighting, ceiling types, and ceiling features, and if any specification changes are necessary during the design phase. Any conflict can cause additional expenses for the relocation or raising of these lines.
Fire Rated partitions are generally indicated above the ceiling, and are rarely seen below the ceiling line, particularly in finished space. Understanding where these partitions are located, and their given rating, can identify design constraints, as well as dictating necessary penetrations for infrastructure. If a penetration is made in a rated partition, that penetration will need to comply with building code for fireproofing. This issue can also increase the value of a construction budget.
Fireproofing at the deck is an essential measure needed to protect the integrity of its structure in certain classifications of buildings. In some cases, fireproofing material can become loose and detach over time, or can be disturbed and removed due to prior construction. It is important to understand if, and how much, material has been removed, in order to capture as part of a construction budget. To comply with building codes, fireproofing material must be replaced where it is no longer present. If it is not incorporated as part of a budget at the beginning, it will come up as an additional expense when revealed during the inspection process.

Things that can be done to mitigate conflicts
By eliminating as many "unknown" issues as possible, the project team can design more effectively and build more efficiently, facilitating on-time delivery within an educated budget. The following is a list of things to consider as you plan:
Incorporate a contingency value within the project cost to cover unforeseen conditions. Contingency percentages typically range between 5% and 10%.
Review the plenum space with the engineer of record prior to design and before construction in order to incorporate necessary changes into the design and address during the pre-construction pricing phase.
As the general contractor, perform a thorough review of the plenum area and provide a list to the subcontractors to include in their costs.
If possible, review the plenum space with the solicited subcontractor group in order to capture necessary works as part of their costs.
Gather historical data from the building management group for issues they have noticed, or any requirements they might have, whether scheduled in the design or not.
Modify design aspects to accommodate the conditions of the space. The first approach will always be an effort to find a way to make new scheduled material work with existing conditions to avoid altering the design. The worst-case scenarios would be to modify a design to work around these issues or completely re-design the area in question.
What's up there will not frighten you if you know what it is. Better preparation will lead to a more successful design and execution.

Chris Holland is the President of ONYX Constructors LLC, a Houston based General Contractor focused primarily on building interior workspaces. You can contact him at cholland@onyxconstructors.com.
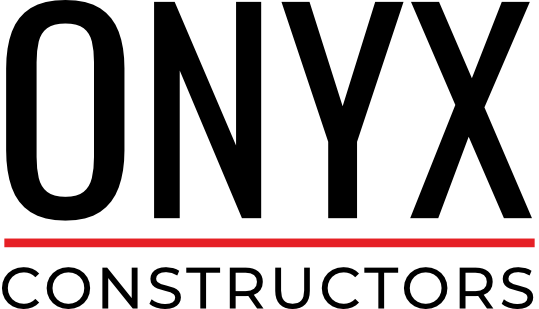
Comments